How Skateboard Decks Are Made: The Process Behind the Ride
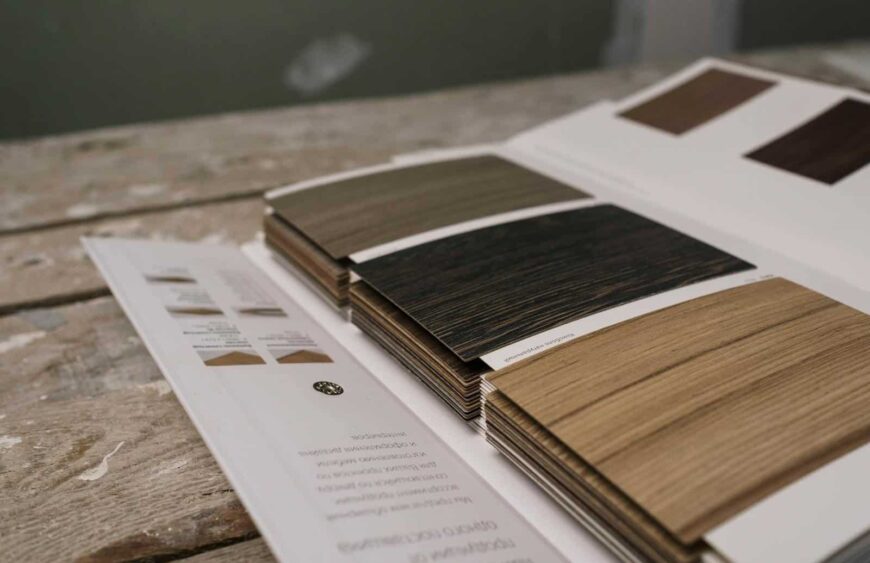
Creating a skateboard deck involves a combination of craftsmanship, science, and creativity. Whether you're riding a street deck, a cruiser, or a longboard, the process behind the creation of these boards is intricate and designed for both performance and durability. Here’s an overview of how skateboard decks are made:
1. Choosing the Right Wood
Most skateboard decks are made from maple wood, particularly hard maple due to its durability and flexibility. The wood is chosen for its ability to withstand the wear and tear of constant impact and grinding. Other woods like birch and bamboo may also be used for specific board types, but maple remains the most popular choice.
Wood Veneers: The wood comes in thin sheets called "veneers." These veneers are carefully selected to ensure they are free from defects and imperfections. Typically, 7-9 layers (plies) of veneer are used for a standard deck, though some high-end boards may have more or fewer plies depending on the desired strength and flexibility.
2. Cutting the Veneers
Once the veneers are selected, they are cut into large sheets. The sheets are then stacked and arranged in a pattern with the grain direction alternating between layers. This process strengthens the board and allows it to withstand the forces a skateboard endures.
Grain Direction: The grain direction of each veneer layer is crucial. Each layer is placed with its grain running perpendicular to the layer beneath it to create the necessary strength and flexibility.
3. Gluing the Veneers
The layers of wood veneers are then glued together using a strong adhesive, often phenolic resin or epoxy glue. This adhesive is applied to each veneer layer before they are stacked together. The stack of veneers is pressed into a mold to form the shape of the skateboard.
Heat and Pressure: The stack is then placed into a hydraulic press that applies both heat and pressure. This helps bond the veneers together tightly, forming a solid piece. The heat also activates the adhesive, ensuring a strong bond between the layers.
4. Shaping the Deck
After the glue has dried and the layers have been pressed together, the skateboard deck begins to take its shape. The excess wood around the edges is trimmed, and the board is cut into the desired shape using a CNC machine (computer numerical control). The CNC machine precisely cuts the outline of the board, including any concave (the curve of the deck) and kicktails (the raised ends of the deck), which are key features for skateboarding.
Concave: Most modern skateboards feature a concave shape. This refers to the curve of the deck from side to side, helping to improve control and making it easier for skaters to perform tricks.
Kicktail: The raised back and/or front of the deck, called a kicktail, is an essential feature for many skateboarding tricks, especially for ollies and flips.
5. Sanding and Refining
Once the skateboard deck is shaped, it undergoes a sanding process to smooth out rough edges and surfaces. This is done to ensure a smooth, comfortable ride and to make sure there are no splinters or sharp spots. This process also ensures that the paint or grip tape adheres properly to the surface.
Hand Sanding and Machine Sanding: The sanding can be done both by hand and using machines to get the perfect finish.
6. Adding Graphics
At this point, the skateboard deck is ready for its graphic design. The deck is either printed or painted with custom artwork, logos, or designs, depending on the brand or the personal preferences of the skater.
Screen Printing or Heat Transfer: Graphics are usually applied using screen printing or heat transfer methods. These methods ensure that the designs are vibrant and durable. For high-end boards, sometimes hand-painted designs are used for a more unique and artistic touch.
7. Applying Grip Tape
Once the graphic is applied and the board is fully cured and dried, the grip tape is added to the top of the deck. Grip tape is a textured adhesive material that provides traction for the skater’s feet, ensuring they don’t slip off the board during tricks or while riding. The grip tape is cut to the shape of the deck, and excess material is carefully trimmed to match the edges.
Adding the Grip Tape: After the grip tape is applied, it is pressed down to ensure it sticks properly and doesn’t lift during use. Skaters may also use a razor blade to make precise cuts around the edges of the board to remove any extra grip tape.
8. Drilling Holes for Trucks
Once the grip tape is applied, the next step is drilling holes for the skateboard trucks. These holes are drilled into the deck using a precise machine, allowing the trucks to be mounted securely. The placement of these holes is essential for the board’s performance, ensuring the trucks are aligned properly for smooth turns and stability.
9. Quality Control
Before the decks are shipped out for sale, they undergo a rigorous quality control process to ensure that the deck meets the required standards for performance and durability. This includes checking the shape, the glue bond, the paint, and ensuring the board is free of defects.
Flex and Durability Test: Some manufacturers even test the flexibility and durability of the deck to ensure that it will withstand the pressures of skating.
10. Ready for the Riders
After passing the quality control checks, the skateboard decks are packaged and ready for sale. Whether they’re sold as blank decks or with custom graphics, they are now ready for skaters to grab and start performing tricks, carving, and cruising.
Conclusion
The process of making a skateboard deck is an intricate and precise series of steps that combines traditional craftsmanship with modern technology. From the selection of high-quality wood to the final touches of grip tape and graphics, every step is essential to creating a board that will perform at the highest level. Whether it’s for a professional skater or someone just getting into the sport, the deck is the foundation of the skateboard, and making it right is crucial for a perfect ride.